RepRap Build
Main > Digital Fabrication > RepLab Tools > RepRap
This page is way way out of date with what is happening with repraps. Basically, the Darwin model is officially a dead end now. Nobody builds these anymore. Nobody uses the electronics below except for Makerbot and they just went proprietary so this whole page is essentially a dead end.
The current model T of repraps is the Prusa Mendel. This is pretty much a run of the mill base reprap. For electronics, use an Arduino Mega with RAMPS 1.4 electronics and Sprinter or Marlin firmware.
For the best high-level overview of how a reprap goes together, see this page:
Ignore most of this from here on down it is ANCIENT
Overview
3D Printer RepRap Build.
Parts
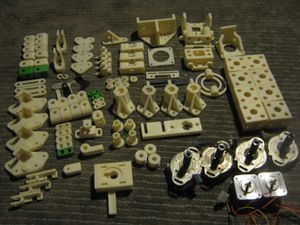
- Frame corners and rods - using 5/16" rod and threaded rod (studs in British)
- Extruder controller - [1]
- [3] Nema 17 motors: 2 for x and y axes, and 1 for extruder - [2]
Frame Rod and Threaded Rod
This work is based on the RepRap master BOM. Its metric system is adapted to retarded Imperial units. We are using 5/16" stock instead of M8.
- xy spacer rod - [1] 355 mm or
- x idler rod - [1] 40 mm
- x motor bracket rod - [2] 520 mm
- xy frame rod - [8] 500 mm
- studding idler studs - [3] 384 mm
- studding drive stud - [1] 260 mm
- vertical post rods - [3] 500 mm
- vertical post rod - [1] 465 mm
- Z axis drive - [4] 275 mm, stainless recommended for straightness and smoothness by HydraRaptor
- base diagonal studs - [2] 660 mm
- Note: All diagonals are studs because they have nuts on ends
- y bearing housing rod - [3] 70 mm
- y idler rod - [1] 472 mm or
- y drive rod - [1] 452 mm or
- side diagonal studs - [8] 660 mm or
- nuts - [32]
- washers - [32]
- M5x8 mm or .20 x .31 in (see Metric to Inch Conversion)
Tools
- Tweezers for surface mount component handling.
- Hot plate
Assembly
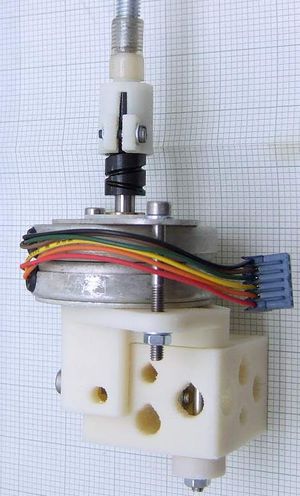
- $8 z axis
- Start with mechanical assembly from RepRap wiki
Notes
On Frame Rods
From Erik:
As long as they're about 8mm in diameter you're good. Everything is designed such that tight tolerances are not required. Part of assembling a machine is taking a series of measurement. You can get away with threaded rods for most of the structural parts, except for the elements that other parts should be able to slide over. Several parts of the frame double as a guide for an axis.
You can also use cheap rod for most of the frame, the sliding ones should be maximally stiff (hardened rod) and chrome coated is nice and shiny. I'm using only the cheap type of ground bars for my own second Darwin, currently. It works fine. You don't need a heavy CNC grade frame when doing additive manufacturing, it's just very inefficient.
On Parts Choices
From Chris Palmer:
We are planning on using the parts shown, including your $8 z axis.
Are the Mother Board v1.1 and Extruder Controller v2.2 the correct boards to use?
The motherboard has moved on to 1.2, but I think the changes are very minor, so 1.1 should work fine. Extruder controller V2.2 is current. You will also need three stepper motor drivers of course.
What do you recommend for the implementation of the extruder?
I would recommend Wade's design: http://reprap.org/wiki/Geared_Nema17_Extruder. You will probably need to make an adapter plate to mount in on the Darwin carriage, but that should be trivial.
You can either bootstrap using the extruder parts I sent you and then print Wade's or I can print you a set of parts for Wade's if you don't want the hassle.
You can make the standard hot end if you have a lathe, but I would recommend the PEEK / PTFE Hybrid from Brian Reifsnider. http://hydraraptor.blogspot.com/2010/05/plumbstruder.html He sells in the forums and on eBay for very reasonable prices.
I see you're selling Mendel parts on Ebay. Is Mendel achieving widespread replicability?
It hasn't achieved the utopian ideal of everybody printing two sets and passing them on for cost yet, but there are a lot more people printing them than ever printed a Darwin. I have printed about 20 sets since April and got prices from £226 to £460 on eBay. A lot of people have printed their own using Makerbots and Rapmans, so I think there will be 100's around already. The eBay prices provide strong motivation for people to print parts and I am staring to see competition driving the prices down.
From Peter Koeleman
The PCBs and components eventually got to me. I am building the Darwin machine to print parts to build my Mendel machine plus a Mendel for Factor e Farm. Because I had ordered the version 1.2 motherboard and cleaned the version 1.1 board, I am going to switch them. Mendel adaptations to the Makerbot boards require removing parts so why not use the already cleaned board?
To link the studding to the z stepper motor assembly I got 8mm coupling nuts and drilled out 1cm deep at one end with a 8.5mm drillbit. The smooth end fits the printed part and allows the studding to be mounted.
From Erik de Bruijn
The latest versions of these boards are fine. Older versions tend to have more users so you'll also find many solutions compatible to these boards (firmware).
You don't need the extruder controller per se, a TIP110 will do (two integrated transistors to control a bigger current from a chip's I/O pins), but the extruder board probably makes life easier (I just use one controller running 4 steppers and temp. control, but there's no reasons to do this if you have all the parts).
> What do you recommend for the implementation of the extruder?
Many people use Wade's extruder (also based on Adrian Bowyers work). It now contains improvements by Nophead too. http://www.thingiverse.com/thing:3462 However it seems you have a direct drive version for a NEMA17 motor. This one is fine to bootstrap Wade/nophead's extruder with. The direct drive version is very good because of its simplicity. If it works it won't break or wear out. It has few parts, don't need to source exotic things. Though it might lack the torque for really fast printing. You can also adapt it to fit a NEMA23 motor by drilling a small sheet of material with the holes, similar to this printed part. Wade's extruder uses a big bolt as a pinch wheel, that also should work pretty well. You can also see if makerbot's newer pinch-wheels will fit the diameter of your motors. Though I'm not sure whether it will fit your direct drive extruder bracket (it has a pretty big boss/hub).
On Frame Structure Lengths
Q. I will read the build instructions and try to figure out these inconsistencies. I imagine I could make it work by making adjustments. Is it safe to make changes in the structure, or is the design shown typically followed exactly?
A. You could change the frame size but you would have to get the table size correct to match, so it would be easiest to make it the correct size. You can change the height pretty easily though.
Q Also, on the SMT electronics attachment - I received the motherboard with the plastic parts already attached, but the SMT components are not yet attached. Do I need to take the plastic parts off, as they will fry upon heating? I have a spare motherboard PCB, so starting from scratch is not too bad.
A. Certainly you need to remove them if you plan to use a reflow with an oven or plate as they will probably melt. You could see what happens and replace them afterwards if you have spares. Also the PCB won't sit flat on a plate with the through hole pins on the back, so won't get proper thermal contact.
A. You could hand solder the SMT parts if you can get to them with the iron. Weird to put the connectors on first. Even with through hole assembly you put the large items on last, so you can get to the small ones.
A. The through hole components were desoldered and SMD components were put on by Bart Bilos, then the big through hole parts were placed back. The Extruder controller board needed a little prosthetic wire and the crystal moved because a bit of circuitry got damaged in the component removal process.
Q. I have this heater plate, 1000W. Is this ok?
A. A lot of people use such things. I think you will struggle to follow the correct solder profile with it, but then a lot of hobbyists ignore that and get away with it. A local reprapper even re-flowed them in a frying pan over a gas ring! I think one board didn't work and she had to replace some of the chips though.
Steps taken at Factor e Farm
- Procuring rod and stud - and cutting to length.
- Shipped parts to Peter Koeleman for him to finish the machine.
The rods and studding weren't shipped to Peter Koeleman. Instead he got a bunch of materials from a local supplier.
Steps taken by Peter Koeleman
To assist Factor-e-Farm building their reprap machine, I'm building their Darwin RepRap. So far I have the needed generation 3 hardware and soldered together some parts that didn't come prefab. I'm using 'off the shelf' hardware from the German RepRap Foundation that doesn't need a lot of work to make life easier and to avoid mistakes. After the Darwin model is finished I will build Mendel RepRaps.
Circuit boards
There are a few circuit boards to build and link together. I will show them and tell a bit about them.
USB to TTL
The interface to the printer is USB with the help of a UM232R unit by FTDI. The interface on the motherboard is 6 pin serial UART which I bought a connector for that I had to merge with the longer (grey) flat ribbon cable. Note the green marking on the connector. Instructions on how to build this is in the RepRap wiki.
RepRap motherboard
The motherboard is bought prefab and doesn't need a lot of work. There are instructions on how to make this more neat in the RepRap wiki but I haven't done this yet. The connector in the USB to TTL image goes on the six pins on the left. The green marking on the connector goes at the top (marked GRN). Full instructions on connecting hardware are in the RepRap wiki.
Extruder controller
The extruder controller is also bought prefab and doesn't need any modifications. The RJ45 connector links to the bottom right RJ45 connector on the motherboard. There is another connection needed which I'll point out later. Full instructions on connecting hardware are in the RepRap wiki.
The extruder controller board needs a solderbridge between AGND and GND. This is simply in the design of the PCB. You won't always be able to program your firmware into the microcontroller without it, leading to nasty bugs.
Stepper motor driver
You need 3 stepper motor drivers, one for each axis. The top of the motherboard has 3 connectors that connect to the "INTERFACE" connector on the stepper motor driver board. To make a cable that connects a stepper motor driver, look in the RepRap wiki. The lengths for each cable is in this picture at the RepRap wiki, shown in centimeters in brackets; so 61cm for the Z cable, 76cm for the Y cable and 88cm for the X cable.
Opto Endstop
The shop I bought the hardware from sold the parts which I had to solder together. I use the RJ45 connectors instead of the recommended stuff at the RepRap wiki site because they're on the stepper driver boards already. Whatever works, works. Each MIN connector on the stepper driver boards connects to an opto endstop, so you'll need 3 completed boards (the store sells parts to build 6 because it's intended to build a Makerbot).
Stepper motors
The stepper motors I got are type NEMA 17 with 80cm of wires. Pretty nice stuff. The label says SY42STH47-1684B, but they are custom made for the shop I got them from. This is their data sheet.
Testing
Once you have the electronics and connected it all, you can run a few tests to see if you did it right. Testing instructions are on the RepRap wiki.
Here are videos of the progress.
Testing RepRap motherboard from Peter Koeleman on Vimeo.
I hooked up the RepRap motherboard from grrf.de to an ATX powersupply and an UM232R chip to the serial interface.
Running the reprap software with CommsDebug set to true continuously dumps information on the console.
Testing RepRap motherboard and extruder board from Peter Koeleman on Vimeo.
I hooked up the extruder controller board to the motherboard and ran the reprap software again with CommsDebug on. Note the T:2 value which was T:0 before when the motherboard couldn't read the (bogus) temperature value yet.
Steppermotors
Unfortunately, the steppers won't step. I have no idea yet why. The motor that I connected gets power from the stepper driver and it locks in place, I can no longer turn the axle by hand. When adjusting the potentiometer on the stepper driver board to feed the motor I can turn it all the way down to where I can turn it by hand again, then up until it locks in place. Feeding more power does not make it step, just humm and get warm, so I should keep the power setting at the lowest level. I should mention that I put in the motherboard firmware from the FiveD_GCode_Interpreter.pde sketch in reprap-mendel-20100806.zip with this configuration.h file. I have not adjusted the motherboard physically, so it runs off a computer power supply, and so do the stepper driver boards. Here's a picture to clarify all wiring:
When I power on the board all LEDs on the stepper board are on all the time instead of blinking when a motor should move. This should be a hint to what is wrong.
Update Well I guess I found out what's wrong, probably my boards aren't manufactured properly. Here's the official support question and answer http://forum.grrf.de/topic/stepper-motor-driver-23-problem Meanwhile, I ordered stepper driver boards for the second machine which function properly. I am waiting for the GRRF boards to come in my mailbox.
Update 2 Stepper boards are fixed now and everything runs.
Building material
The Mendel machine has a lot of nuts, bolts and washers. I ordered a hardware kit from http://www.mendel-parts.com/ that has all the hardware to build the frame and moving parts, except for some parts for the extruder like nichrome wire.
To cut the rods and studding I made myself a simple workbench from stuff laying around the house. I include a picture to show you can easily cut stainless steel with a handsaw. I used up two sawblades though, which cost me about €5 but I saved €20 from the mendel parts shop.
To measure the studding and rods I put tape on the measuring tool first and held the studding alongside to transfer the tape. This is how I made sure the tape was on straight. Start sawing in the studding groove. Give yourself about half a milimeter extra and file down the sawn edge to the right size, making it nice and smooth. Keep measuring after each step to make sure you're not adding up little offsets.
And here is the finished product (which I'm kind of proud of). Cut to size and labeled. I don't have the printed parts yet, so I'm going to have to store these for a while.
For the thick sheet material I found a leftover of Trespa panel. I printed out the DXF files using QCad and pasted those paper prints onto the sheet material. I used a paper glue pen which is easily removed from the Trespa afterwards. Using a mounted drill I drilled all 4,5mm and 3,5mm holes first and then sawed the rest of the shapes. Trespa is very easy to drill in but remember to use a fine sawblade. The printbed is aluminum and slightly bigger than the DXF file suggests because I might want to make it into a heated printbed. I got the material from a local metal workshop that sold me the 232 by 260 mm plate for €5. It was an arbitrary price I think, they have lots of small pieces around the shop and they only had to cut it for me. I drilled holes and filed away the sharp edges.
Here's the finished sheet stuff:
The Darwin model
I started building RepRap Darwin. I follow the building instructions at http://reprap.org/wiki/AssemblingDarwinMachinery which are very detailed. Instructions for the Z axis can be found at Chris' site.
Here's a picture of the build in progress:
I tried printing a few small shapes: http://www.thingiverse.com/thing:2653
This is what I got:
To improve the Y axis to move smoothly, I installed a bearing and I wrapped some PTFE tape around the reprapped parts that fix the carriage on the steel rods. To improve the X axis I swapped the motor for one of these.
After improving the axis movement and having a gear wheel adapted to fit the stepper motor I made another test print. I did not print on a raft this time and the results are improving. The first print (bottom) was with higher extruder speed. The second print (top) was at 1000mm/min extrusion speed which seemed to improve print quality.
The reprap software works for sending g-code to the printer, warming up and moving the printhead around. The g-code generated bij skeinforge works better for me. It's easy to load the g-code into the reprap software and print on a preheated printer. The nozzle needs to have extruded an amount of plastic to flow well enough to print with.
Extruders
There is a lot of innovation going on in extruders. I will need to decide which model works best for me and get the parts for three machines. Erik de Bruijn (another True Fan) has offered to help! There is a simple extruder which I have parts for, so I'll build that first and then see if I need to and can improve print quality with another extruder model.
Testing the nichrome wire:
Note that the wire should be connected to the terminal closest to the RJ45 connector on an actual printer.
Extruder replacement
After trying to get the extruder to work and failing, I scratched the extruder design and ordered in an extruder kit. Made from wood on a laser cutter, but it works great.
Issues
Using the new extruder solved the extruder issues, but the 4 motor z axis problems are not all gone. The z axis still does not want to stay synchronized because sometimes one of the motors stutters. The extruder is now mounted on the carriage, but I'm looking into making an extruder with a bowden cable to drive the extruder head better.
RepRap Mendel printed parts
I am currently printing Mendel parts. Quality is sufficient, some improvement may be needed for some of the parts.
The last step will be to construct an extra Mendel machine for Factor e Farm because with self replicating hardware it's a good idea to have a spare.