The Liberator Full Release - Mechanical Fabrication: Difference between revisions
(→Frame) |
(→Frame) |
||
Line 32: | Line 32: | ||
After drilling, the frame is bolted together, Fig. 3. After bolting the frame can stand vertically, ready for attachment of the arms, Fig. 4. | After drilling, the frame is bolted together, Fig. 3. After bolting the frame can stand vertically, ready for attachment of the arms, Fig. 4. | ||
[[Image:framebolted.jpg|thumb|Fig. 3. Frame bolted together.]] | |||
[[Image:framestanding.jpg|thumb|Fig. 4. Frame standing.]] | [[Image:framestanding.jpg|thumb|Fig. 4. Frame standing.]] | ||
==Cylinder Attachment== | ==Cylinder Attachment== |
Revision as of 22:10, 2 June 2010
Frame
The frame consists of 7/16" thick, 6" wide u-channel. The frame is the same as that found in Prototype 1. You can use that as a fabrication guide. See the pictures 1-3 of CEB_Prototype_1_Fab.
The Liberator Beta v2.0 is fabricated as follows. First, see the technical drawing for the overview:
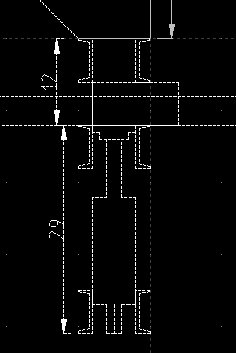
The u-channels are shown around the cylinder and below the hopper.
Here are some fabrication pictures:
Frame
The frame is design-for-disassembly. 1/2" bolts, grade 8, are used to hold the frame together. The main cylinder attaches to the bottom of the frame, and the opposing members are at the top of the frame. These sets of frame members withstand the entire pressure of the cylinder, 20 tons, with the use of 8 bolts. Thus, each bolt needs to withstand about 5,000 lb of shear force. The area of a 1/2" bolt (.2 sq in) at over 100ksi strength, indicates 20,000 lb shear force per bolt, or a safety factor of 4. The middle set of structural u-channel members do not undergo shear force, but only expansion force of the soil as it is pressed in the compression chamber.
The structural members of the frame are 8 in number. The verticals (2), bottom cylinder support (2), opposing support (2), and compression chamber (2). There are 2 non-structural u-channels (8" wide), which close the bottom part of the compression chamber, with little force acting against them. These are 1/4" thick, while all the other structural members are 7/16" thick.
Fig 1 shows the frame members, being aligned for Transfer Punching holes for the 1/2" bolts. The dimensions of the u-channel members are shown in the technical drawing referred to above - see frame_overview.dxf (94.2 KB) from 01/20/2010 03:36 pm at Open+Pario.
Clamp all the structural members together, while fitting the soil drawer (shown further down) to assure correct spacing. Transfer punch all the holes with machine positioned vertically so that all holes are accessible. See Fig. 2.
Holes in the eight, short, u-channel members have already been punched with a 120 Ton Hole Puncher or similar, with capacity to punch 9/16" holes. The holes are 9/16" - as 1/2" punched holes would be slightly undersized.
The two, vertical u-channels are then drilled at the location of the transfer punch marks.
After drilling, the frame is bolted together, Fig. 3. After bolting the frame can stand vertically, ready for attachment of the arms, Fig. 4.